Expert Analysis Writer: Brandon Kinsey, district sales manager at CENTRIA
Exceeding Expectations: The All-In-One Wall System
The building envelope – and how it is constructed and installed – has substantial impact on any structure’s appearance and its long-term performance. Architects, designers, builders, installers, and other construction stakeholders must take a variety of factors into account when deciding on a building envelope solution – aesthetic impact and curb appeal, installation requirements, construction schedules, energy efficiency throughout the life of the building, and durability against the elements.
It begins in the design process.
Insufficient air barrier detailing often occurs at transitions in wall materials, roofing, or windows. The lack or misplacement of an air barrier allows for thermal bridging through window framing, insulated glass units, components, or sub framing.
Even a perfectly designed multi-component wall system will look and perform only as well as those who install it. The variables are nearly endless – laborers who do not possess the requisite skills, workers that are not properly trained or supervised, or lack of coordination on the job site amongst multiple trades. Taken together, this means that installation errors can heavily impact a building’s longevity.
When a barrier fails, who is responsible? The architect? The contractor? The installer?
When insulated metal panels (IMPs) are specified as the all-in-one wall system for a building envelope, many of these variables are eliminated. IMPs are built to integrate seamlessly with any materials, increasing building performance and aesthetics.
Built to Perform
A traditional wall system is typically comprised of stud framing, air and vapor barriers, rigid insulation, and the exterior cladding component. For the most part, these multi-component systems require a high level of detail, leaving room for performance setbacks. IMPs do not need a backup wall assembly to keep air, water, or vapor out. IMPs are an all-in-one wall system, comprised of two steel skins and a liner that that are typically G-90 galvanized. Rigid foam insulation binds the two sheets of metal together. Integrated components withIMP systems maximize thermal and moisture protection with engineered, pressure-equalized joinery, concealed sealants, and a built-in vapor barrier.
The backside of an IMP liner is a metal G-90 liner that is typically a 26-gauge panel, forming an effective air barrier that is then married into a non-skinning butyl for complete adhesion of the air barrier. The continuous water barrier, a rainscreen, is on the exterior side of the panel. With the help of a slope joinery, the water will hit the panel and simply drain downward.
Insulation value is a driving factor for architects and building owners to consider specifying IMPs for a project. The insulation value varies based on the thickness of the panel. Typically, architectural IMPs are manufactured with polyisocyanurate, which helps IMPs hold an R-value of R-7 per inch. Compared to other commonly used insulation materials like mineral wool, IMPs guarantee almost double the R-value that can be assigned to the building envelope.
Insulated metal panels can be made one of two ways – laminated or foam-in-place.
With laminated IMPs, the manufacturing process begins with taking the exterior sheet and roll forming it into the desired shape followed by the same process on the liner side. Then, workers take a board stock insulation and glue it to the steel skins to laminate the three pieces together. Laminated panels are best reserved for customized applications.
Foam-in-place panels have the liner and face sheet rolled in place with a liquid-applied foam to fill the gaps between the two sheets. The process creates a superior bond, filling all voids and producing excellent panel flatness.
Meeting the Standard
Architects. contractors, building owners, and installers are under pressure to ensure today’s buildings are sustainable and energy efficient. When specifying building products, the first question often on a project manager’s mind is: How well will it perform? When it comes to specifying the right product for a facade, the design team weighs a variety of factors, including building usage, location, energy efficiency, thermal performance, costs and more.
IMPs can contribute to energy performance and recycled content credits for a project, including LEED certification. IMPs are manufactured using highly recyclable steel, meaning the product can be made of up to 90% recycled content. The use of an electric arc furnace (EAF) is a more sustainable method for steelmaking as they emit fewer pollutants and greenhouse gases, reducing the environmental footprint.
Today, many building material manufacturers are pushing toward overall carbon footprint reduction, with many aiming for net zero emissions. How are architects and manufacturers making a difference?
Specifying insulated metal panels (IMPs) for a project preserves an architect’s flexibility in terms of design and performance, while also providing a wide range of sustainability benefits.
The Desired Look and Feel
With every project, architects and designers are consistently seeking products that will help them deliver the look and feel they envision on paper. While performance is a top consideration when building or renovating a space, a project team has a variety of factors to consider: Is the material weather resistant? Is it available in the desired colors? Will it require constant maintenance to retain its look? How will the exterior meet the desired vision?
Insulated metal panels meet the demands of not only performance but also unlimited design freedom for architects. When thinking about IMPs, often a plain, flat panel comes to mind. With today’s IMPs, a wide variety of colors, profiles, lengths, and widths are available that can help bring any architect’s vision to life. The versatility of the panels allows designers to create multiple styles and looks that can be integrated across the building envelope.
Simplifying the Process
Construction stakeholders of every kind are under constant pressure to finish a job as quickly and efficiently as possible. Multi-component building envelope systems require the coordination of multiple trades for installation, which can often expand a project timeline and involve additional costs. With an integrated component system such as an IMP, a construction manager writes one contract for the full building envelope, condensing the contracting process. With one installer for wall panels, windows, louvers, accent fins and sunshades, there is less liability and a simpler installation schedule. Rather than coordinate multiple trades on site, the building can be enclosed with a single installer.
In addition, utilizing IMPs means fewer structural supports are needed, which is crucial to long-lasting appearance. The panels can span long distances while maintaining and increasing building enclosure durability due to the multi-layer design. This saves costs on materials and simplifies building engineering.
Consider the case for the Hyatt Regency in Salt Lake City. The 26-story, 700- room hotel needed to accommodate a busy, tight urban location with limited places to stage equipment and materials. This required a fast-paced construction schedule. Designers needed a material that could be installed quickly while also integrating with the glass curtainwall. IMPs fit the bill on all fronts – labor reduction, ease of installation, and ability to integrate.
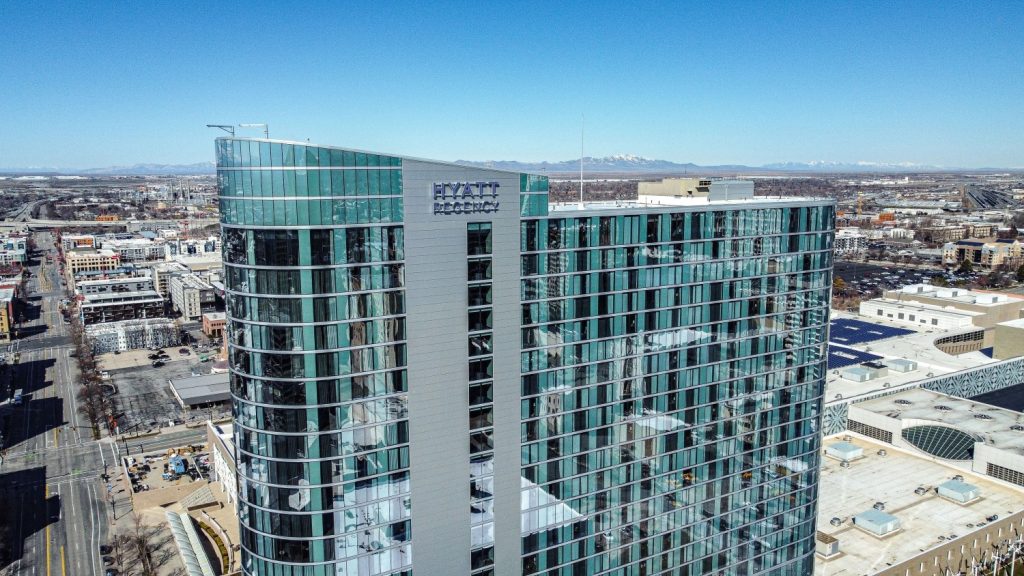
Integration Made Easy
IMPs integrate seamlessly into windows, sunshades, louvers, and daylighting to deliver a seamless, high-performance building envelope. Window joinery is fully engineered to integrate with the metal panel joinery, eliminating the need for receptor extrusions and exposed sealants. The thermal performance of a typical window is significantly less than one that is fully integrated at the window head. The fully integrated window system also provides a clean façade with no extra flashings, maintaining the architect’s desired look.
Sunshades can be used to significantly reduce building heat gain from solar radiation, while maintaining opportunities for daylighting, views, and natural ventilation. If the shading is from an internal device, solar gain through a window can be reduced up to 80%, increasing energy efficiency, and lowering cooling costs for the building.
Making the Case-St. Josephs Candler Hospital
Saint Joseph’s/Candlers (SJ/C) Hospital in Savannah, Georgia is comprised of two of the longest-standing hospitals in the United States. The building needed a facelift, including a building envelope solution that eliminated water intrusion, provided wind resistance, and thermal efficiency.
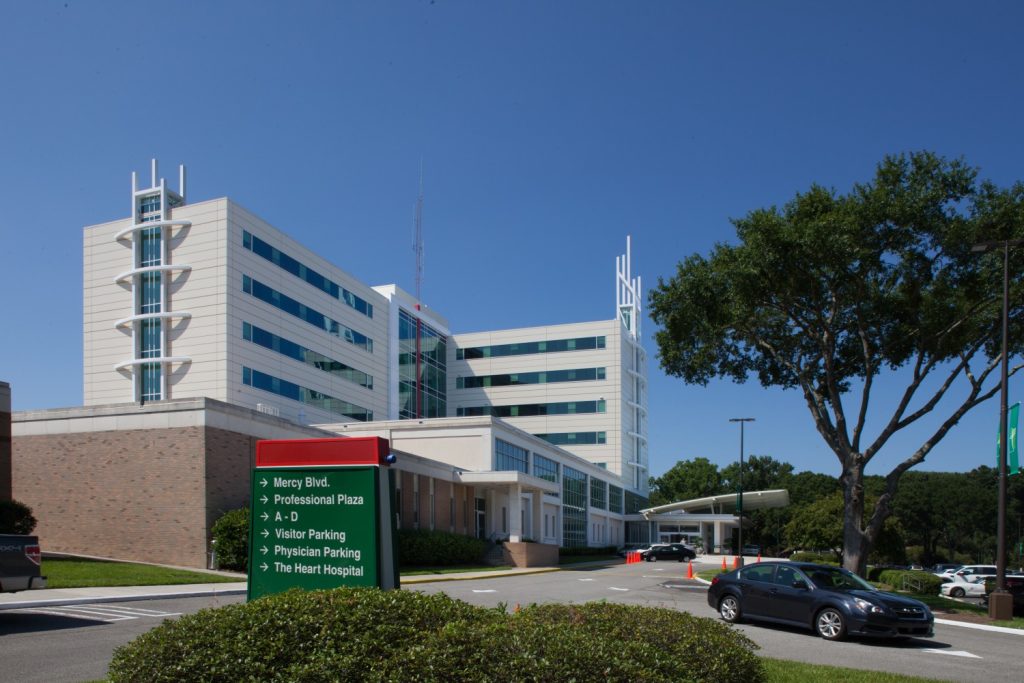
The upgrade also had to be handled in a way that would not interrupt hospital operations, enabling the facility to continue providing care. With an insulated metal panel system and integrated windows, the new facade accommodated an accelerated construction schedule that enabled care to continue. In addition, the IMPs seamlessly integrated with the new windows. The detailed intersections and edges of the insulated metal panel system brought a new level of integration to the project.
Specifying a Simpler Solution
Consider the following when selecting insulated metal panels: ease of detailing, long-term weathertightness, and enhanced energy efficiency. IMPs can accommodate high-quality views, daylighting, and ventilation, integrating directly with joinery of the panels. By eliminating the need for detailing component/wall interfaces, IMPs simplify and accelerate the construction process while providing virtually unlimited design freedom.
From the contractor managing the job to the installers, the building owners, and eventual inhabitants of the structure, the entire project team benefits from designing with IMPs. IMPS have grown to be the faces of sports arenas, office buildings, healthcare facilities, schools, museums, and more. No matter the market, insulated metal panels are an all-in-one cladding solution for architectural, commercial, and institutional markets.
About the Author:
Brandon Kinsey is the district sales manager at CENTRIA in the greater Detroit area. He earned a bachelor of science degree in construction management from Eastern Michigan University, and has served as a member of CENTRIA’s insulated metal panel (IMP) product development team.